From the Bottom Up: LEAN Translates into Better Customer Service
By Sylvain Laporte, Chief Executive Officer, Canadian Intellectual Property Office
The customer is always right. Le client n’a jamais tort. Der Kunde ist König.
In any language, in any country, this motto has long been the cornerstone of the service industry – where client satisfaction alone can mean the success or failure of a business.
In recent years, governments around the world have seen the wisdom of this private sector thinking and are taking a more customer-centric approach to service delivery.
Here at the Canadian Intellectual Property Office (CIPO), we are no different. We know our customers want value for money in using our services. To make this happen, we needed to carefully review our office practices, find ways to improve them and eliminate activities that do not provide value. This is not an easy task.
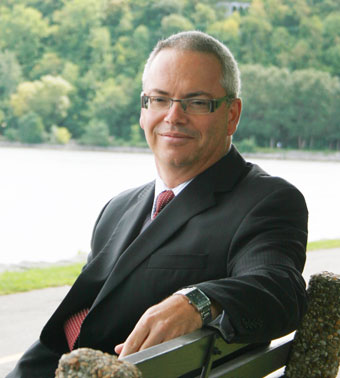
Intellectual Property Office.
That is why we decided to apply the LEAN methodology, and we’re excited by the early results.
In just 24 months, we have developed our internal competencies, run multiple prototypes and instilled a customer-centric culture that will continue to enable the transformation process. With LEAN firmly established in the organization, we:
- reduced a part of the trademarks registration process from 7 to 2 days;
- cut our lead time for patent applications (how we sort, validate and scan incoming applications) from 400 to 24 hours;
- increased our quality control by checking 100 percent of items, up from 50 percent;
- dropped our patent exam report lead time (how long it takes to reach a client) from 13 to 3 days; and
- applied a continuous flow process for our patent exams, thereby leveling the production load.
So, what is LEAN?
Put simply, LEAN is a grassroots way for an organization to continuously improve the timeliness, quality and cost-efficiency of business operations. Always with the customer in mind, LEAN relies on its frontline staff to be the catalysts for change. Employees are directly involved in sharing ideas on how to increase customer value, from one end of a process to the other.
This notion is at the core of LEAN, a management approach originally developed in the manufacturing industry and now being applied across a wide variety of industries and government.
Why go LEAN?
When we first considered the concept of LEAN, there was the usual mix of fear and doubt associated with any organizational change. Is it sustainable? How much time and effort will it take?
Applying LEAN takes discipline, flexibility, tenacity, and most of all, the drive to be better. With this in mind, we knew LEAN was the key to:
- empowering CIPO employees to find efficiencies in their work;
- reducing lead time with our customers by eliminating redundant work processes;
- enabling us to respond more promptly to customers while improving quality and cost-effectiveness; and
- creating a culture of ongoing improvement that has all employees constantly thinking of better ways to do their work.
It is so easy to lose sight of the customer, but the LEAN method reminds us to put the vision of customer service back into focus.
Setting the foundation
Recognizing the need to improve operating efficiency, a few years ago, CIPO implemented a LEAN education program to engage and develop employees as LEAN agents. While this requires investment in employees, it certainly pays off as it encourages employees themselves to invest in improving the organization. Those taking part in the program can obtain industry-recognized certification at several progressive levels. Building our own internal expertise means that future change will be driven by our workforce.
Although at first, some employees were unsure about LEAN, the benefits of “having a voice” were quickly recognized. Participation continues to grow across CIPO.
Building on success
Since the LEAN mindset is about trusting employees (rather than management) to drive change, employee morale has improved. We are receiving positive feedback across the organization, and seeing a positive shift in perception as employees understand and engage with the processes they work on every day.
Our first group of LEAN agents and their teams have achieved incredible productivity gains, reduced turnaround times and improved quality. We now have 28 LEAN agents working with our frontline employees in all sectors.
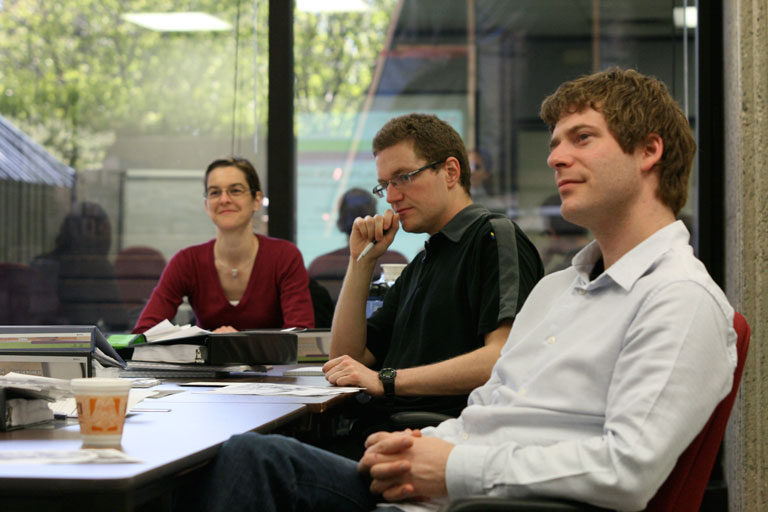
Next steps
Our ultimate goal is to “LEAN” the entire organization. Buoyed by positive results and rapid progress, LEAN is becoming engrained in CIPO’s culture. We have seen how the “bottom-up” approach enables employees to influence their work and how they do it. This, in turn, will drive them to aim higher and deliver even better customer service.
Improving the business of an organization is never easy; we have certainly experienced our share of growing pains. But thanks to our drive and commitment – a conviction that everything can be improved – and the notion that nothing is exempt from improvement, we are seeing concrete efficiency gains as well as improvements in the overall quality of our customer service and employee morale.
So, yes, the customer is always right. But sometimes we public servants get it right, too.
For more information on the LEAN process, visit http://www.lean.org/.
The WIPO Magazine is intended to help broaden public understanding of intellectual property and of WIPO’s work, and is not an official document of WIPO. The designations employed and the presentation of material throughout this publication do not imply the expression of any opinion whatsoever on the part of WIPO concerning the legal status of any country, territory or area or of its authorities, or concerning the delimitation of its frontiers or boundaries. This publication is not intended to reflect the views of the Member States or the WIPO Secretariat. The mention of specific companies or products of manufacturers does not imply that they are endorsed or recommended by WIPO in preference to others of a similar nature that are not mentioned.